News
BLOGS
Apr 14 / 2025
What Is Laser Welding?Applications,Advantages,and How It Works!
Discover laser welding’s precision, applications, and benefits. Learn how Teeming Machinery enhances manufacturing efficiency and quality.
Laser welding revolutionizes modern manufacturing with its ability to create precise, strong, and clean welds. This innovative technique uses concentrated laser energy to fuse materials, providing unmatched accuracy and efficiency.
From aerospace to medical device production, laser welding is reshaping industries by offering flexibility and reliability in joining a variety of different materials. By understanding its principles, applications, and benefits, businesses can make informed decisions about integrating this technology into their operations.
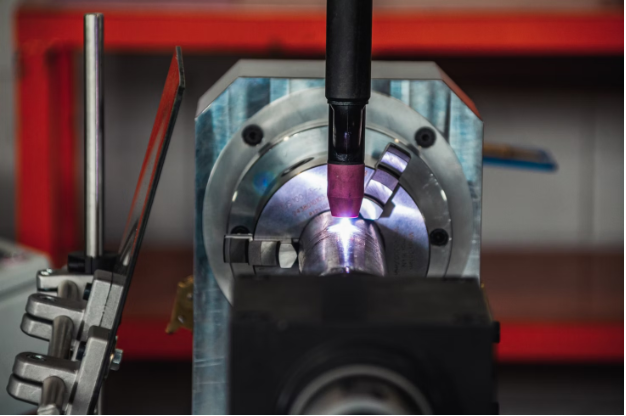
An Introduction to Laser Welding and Its Principles
Laser welding is a highly precise and efficient method for joining materials using concentrated laser energy. By focusing a high-intensity laser beam onto a small area, this process melts and fuses materials together with exceptional accuracy. Laser welding is widely regarded as a cutting-edge technique in modern manufacturing, offering both flexibility and consistency for numerous applications.
This method of joining is suitable for a wide range of materials, including metals and certain plastics. Its ability to generate a small heat-affected zone minimizes distortion and makes it an attractive option for industries that demand precision, such as aerospace and medical device manufacturing. The process involves the use of various laser types, including fiber, CO2, and Nd:YAG lasers, each chosen based on the material and application.
Teeming Machinery specializes in providing advanced laser welding solutions tailored to meet the needs of diverse industries. With cutting-edge technology and expert support, Teeming helps businesses achieve unparalleled precision and efficiency. Contact our specialists at Teeming Machinery today to explore how their innovative equipment can elevate your manufacturing capabilities and streamline your production processes.
The Most Common Materials That Can Be Welded Using Laser Welding
Laser welding is a versatile technology that works effectively with a wide range of materials, making it a valuable asset in numerous industries. From metals to plastics, laser welding accommodates diverse materials, each chosen for specific applications where performance and durability are paramount.
Whether it's creating intricate jewelry, assembling aerospace components, or fabricating medical devices, laser welding provides a reliable solution for even the most demanding applications.
Advantages of Laser Welding
Laser welding offers numerous advantages over traditional welding techniques, making it a preferred choice for industries that demand high-quality results.
One major advantage is the precision it provides. The focused nature of the laser beam allows for exact control, resulting in minimal waste and reduced need for post-weld machining.
Another significant benefit is the ability to work at high speeds which reduces production times without sacrificing quality. This efficiency makes it ideal for mass production settings, such as automotive manufacturing. Laser welding can also join dissimilar materials, enabling creative solutions for modern design and engineering challenges.
The process also produces clean welds that require little to no additional finishing. Since the laser creates a small heat-affected zone, it reduces thermal damage to surrounding materials. This feature is especially important in industries where maintaining the structural integrity of delicate components is critical.
Summary of Advantages
Laser welding finds applications across a variety of industries thanks to its adaptability and precision.
Regardless of the industry or application, laser welding is an indispensable tool for modern manufacturing. Its precision, speed, and adaptability make it a go-to solution for creating reliable and high-quality joints across a wide range of materials.
Key Points to Note During Laser Welding
Selecting the Right Type of Laser
Choosing the correct laser type is essential for achieving the best results in laser welding. Different materials and applications require different types of lasers to ensure effective fusion and minimize errors.
Fiber lasers are particularly well-suited for highly reflective metals, such as aluminum and copper, due to their efficiency and adaptability. On the other hand, CO2 lasers are ideal for working with non-metallic materials, such as certain plastics, and provide a reliable solution for industries like packaging and medical devices.
Aligning and Focusing the Laser Beam
Proper alignment and focusing of the laser beam are critical steps in ensuring high-quality welds. Misalignment can lead to weak or uneven welds, potentially compromising the strength and durability of the joint.
Operators must carefully calibrate the laser system to maintain a consistent beam path, which is essential for precision. Focusing the laser beam correctly also reduces the risk of damaging the surrounding material, helping to preserve the integrity of the workpiece.
Controlling Welding Parameters
Effective control of welding parameters, including beam intensity, welding speed, and shielding gas flow, is vital to the success of the laser welding process. Beam intensity must be adjusted based on the material thickness and composition to prevent overheating or under penetration.
Welding speed also plays a significant role in determining the strength and appearance of the weld, while shielding gas helps protect the molten material from oxidation and contamination to ensure a clean and robust joint.
Ensuring Safety Measures
Safety is a top priority in laser welding due to the potential hazards associated with high-intensity laser beams. Operators must wear appropriate protective equipment, such as laser safety goggles and gloves, to prevent injuries.
Proper ventilation systems are also crucial for managing fumes and particles generated during the welding process, especially when working in confined spaces. Following established safety protocols not only protects workers but also contributes to maintaining a secure and efficient workplace environment.
Maintaining Equipment and System Calibration
Regular maintenance and calibration of laser welding equipment are essential to ensure consistent performance and prevent downtime. Over time, components like lenses and mirrors can accumulate debris or experience wear, affecting the quality of the weld.
Periodic inspections and cleaning help keep the system in optimal condition, while software updates can improve operational efficiency and introduce new capabilities.
Adapting to Specific Material Properties
Different materials have unique properties that influence their behavior during welding. For example, materials with high thermal conductivity, such as copper, may require specific adjustments in laser intensity and speed to achieve effective welds.
Understanding these nuances enables operators to adapt their approach and achieve strong, reliable joints regardless of the material being welded.
Teeming’s Advantages in Laser Welding
Advanced Technology and Expertise
Teeming Machinery stands out as a leader in providing cutting-edge laser welding solutions for industries worldwide. The company’s expertise in fiber laser technology ensures high-quality results for complex applications. By integrating innovative techniques and advanced systems, Teeming continually delivers unparalleled performance and reliability to its clients.
User-Friendly and Versatile Machines
Teeming’s laser welding machines feature intuitive interfaces and advanced capabilities, making them ideal for both small-scale operations and large industrial projects. Their flexibility allows manufacturers to achieve high-quality results across a variety of materials and applications, ensuring seamless adaptation to evolving industry demands.
Commitment to Customer Success
Teeming provides comprehensive support services, from initial consultation to ongoing maintenance, helping clients optimize their manufacturing processes and stay competitive. The company prioritizes long-term relationships, ensuring customers have access to expert advice and tailored solutions throughout their journey.
Competitive Pricing and Cost-Efficiency
Teeming offers cost-effective solutions without compromising quality, helping businesses maximize their return on investment. By delivering high-performance equipment at competitive prices, Teeming supports manufacturers in achieving their production goals while controlling costs.
Sustainability and Innovation
Teeming is committed to sustainable practices, incorporating energy-efficient technologies into its machines. This dedication to innovation not only benefits the environment but also provides customers with advanced tools that meet modern sustainability standards.
Contact Teeming Today
At Teeming Machinery, we're dedicated to helping you achieve precision and efficiency in your manufacturing processes. Our state-of-the-art laser welding technology and expert support services are designed to meet the needs of industries like automotive, aerospace, and medical device manufacturing.
Contact us today to learn how our innovative solutions can enhance your production capabilities and keep you ahead in a competitive market.
Laser welding revolutionizes modern manufacturing with its ability to create precise, strong, and clean welds. This innovative technique uses concentrated laser energy to fuse materials, providing unmatched accuracy and efficiency.
From aerospace to medical device production, laser welding is reshaping industries by offering flexibility and reliability in joining a variety of different materials. By understanding its principles, applications, and benefits, businesses can make informed decisions about integrating this technology into their operations.
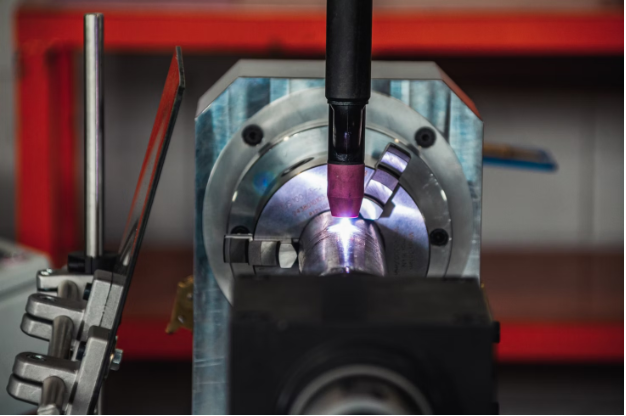
- An Introduction to Laser Welding and Its Principles
- Advantages of Laser Welding
- Common Applications and Industries for Laser Welding
- Key Points to Note During Laser Welding
- Teeming’s Advantages in Laser Welding
- Contact Teeming Today
An Introduction to Laser Welding and Its Principles
Laser welding is a highly precise and efficient method for joining materials using concentrated laser energy. By focusing a high-intensity laser beam onto a small area, this process melts and fuses materials together with exceptional accuracy. Laser welding is widely regarded as a cutting-edge technique in modern manufacturing, offering both flexibility and consistency for numerous applications.
This method of joining is suitable for a wide range of materials, including metals and certain plastics. Its ability to generate a small heat-affected zone minimizes distortion and makes it an attractive option for industries that demand precision, such as aerospace and medical device manufacturing. The process involves the use of various laser types, including fiber, CO2, and Nd:YAG lasers, each chosen based on the material and application.
Teeming Machinery specializes in providing advanced laser welding solutions tailored to meet the needs of diverse industries. With cutting-edge technology and expert support, Teeming helps businesses achieve unparalleled precision and efficiency. Contact our specialists at Teeming Machinery today to explore how their innovative equipment can elevate your manufacturing capabilities and streamline your production processes.
The Most Common Materials That Can Be Welded Using Laser Welding
Laser welding is a versatile technology that works effectively with a wide range of materials, making it a valuable asset in numerous industries. From metals to plastics, laser welding accommodates diverse materials, each chosen for specific applications where performance and durability are paramount.
- Steel: Widely used in industrial applications due to its strength and compatibility with laser welding.
- Aluminum: A lightweight material often used in aerospace and automotive industries.
- Titanium: Frequently employed in medical devices and aerospace components for its durability and corrosion resistance.
- Nickel alloys: Common in high-performance applications like jet engines and power plants.
- Copper: Known for its high thermal and electrical conductivity, suitable for electronics manufacturing.
- Plastics: Select polymers used in medical equipment or automotive components.
- Precious metals: Such as gold and silver, used in jewelry and electronics manufacturing.
Whether it's creating intricate jewelry, assembling aerospace components, or fabricating medical devices, laser welding provides a reliable solution for even the most demanding applications.
Advantages of Laser Welding
Laser welding offers numerous advantages over traditional welding techniques, making it a preferred choice for industries that demand high-quality results.
One major advantage is the precision it provides. The focused nature of the laser beam allows for exact control, resulting in minimal waste and reduced need for post-weld machining.
Another significant benefit is the ability to work at high speeds which reduces production times without sacrificing quality. This efficiency makes it ideal for mass production settings, such as automotive manufacturing. Laser welding can also join dissimilar materials, enabling creative solutions for modern design and engineering challenges.
The process also produces clean welds that require little to no additional finishing. Since the laser creates a small heat-affected zone, it reduces thermal damage to surrounding materials. This feature is especially important in industries where maintaining the structural integrity of delicate components is critical.
Summary of Advantages
- High precision reduces waste and post-weld machining requirements.
- Fast processing speeds support high-volume production.
- Ability to join dissimilar materials enables innovative designs.
- Minimal heat-affected zone preserves material integrity.
- Clean welds often eliminate the need for additional finishing.
Laser welding finds applications across a variety of industries thanks to its adaptability and precision.
- Automotive: Used to assemble car doors, exhaust systems, and battery casings, ensuring high production speeds and strong joints.
- Medical devices: Creates surgical tools, implants, and contamination-free welds for hygiene-critical applications.
- Aerospace: Joins lightweight materials like aluminum and titanium for aircraft and spacecraft components.
- Electronics: Welds delicate parts such as sensors, connectors, and micro-components with high precision.
- Jewelry: Repairs and fabricates intricate designs in gold, silver, and other precious metals.
- Energy: Used in power plants and renewable energy applications, such as wind turbine assemblies.
Regardless of the industry or application, laser welding is an indispensable tool for modern manufacturing. Its precision, speed, and adaptability make it a go-to solution for creating reliable and high-quality joints across a wide range of materials.
Key Points to Note During Laser Welding
Selecting the Right Type of Laser
Choosing the correct laser type is essential for achieving the best results in laser welding. Different materials and applications require different types of lasers to ensure effective fusion and minimize errors.
Fiber lasers are particularly well-suited for highly reflective metals, such as aluminum and copper, due to their efficiency and adaptability. On the other hand, CO2 lasers are ideal for working with non-metallic materials, such as certain plastics, and provide a reliable solution for industries like packaging and medical devices.
Aligning and Focusing the Laser Beam
Proper alignment and focusing of the laser beam are critical steps in ensuring high-quality welds. Misalignment can lead to weak or uneven welds, potentially compromising the strength and durability of the joint.
Operators must carefully calibrate the laser system to maintain a consistent beam path, which is essential for precision. Focusing the laser beam correctly also reduces the risk of damaging the surrounding material, helping to preserve the integrity of the workpiece.
Controlling Welding Parameters
Effective control of welding parameters, including beam intensity, welding speed, and shielding gas flow, is vital to the success of the laser welding process. Beam intensity must be adjusted based on the material thickness and composition to prevent overheating or under penetration.
Welding speed also plays a significant role in determining the strength and appearance of the weld, while shielding gas helps protect the molten material from oxidation and contamination to ensure a clean and robust joint.
Ensuring Safety Measures
Safety is a top priority in laser welding due to the potential hazards associated with high-intensity laser beams. Operators must wear appropriate protective equipment, such as laser safety goggles and gloves, to prevent injuries.
Proper ventilation systems are also crucial for managing fumes and particles generated during the welding process, especially when working in confined spaces. Following established safety protocols not only protects workers but also contributes to maintaining a secure and efficient workplace environment.
Maintaining Equipment and System Calibration
Regular maintenance and calibration of laser welding equipment are essential to ensure consistent performance and prevent downtime. Over time, components like lenses and mirrors can accumulate debris or experience wear, affecting the quality of the weld.
Periodic inspections and cleaning help keep the system in optimal condition, while software updates can improve operational efficiency and introduce new capabilities.
Adapting to Specific Material Properties
Different materials have unique properties that influence their behavior during welding. For example, materials with high thermal conductivity, such as copper, may require specific adjustments in laser intensity and speed to achieve effective welds.
Understanding these nuances enables operators to adapt their approach and achieve strong, reliable joints regardless of the material being welded.
Teeming’s Advantages in Laser Welding
Advanced Technology and Expertise
Teeming Machinery stands out as a leader in providing cutting-edge laser welding solutions for industries worldwide. The company’s expertise in fiber laser technology ensures high-quality results for complex applications. By integrating innovative techniques and advanced systems, Teeming continually delivers unparalleled performance and reliability to its clients.
User-Friendly and Versatile Machines
Teeming’s laser welding machines feature intuitive interfaces and advanced capabilities, making them ideal for both small-scale operations and large industrial projects. Their flexibility allows manufacturers to achieve high-quality results across a variety of materials and applications, ensuring seamless adaptation to evolving industry demands.
Commitment to Customer Success
Teeming provides comprehensive support services, from initial consultation to ongoing maintenance, helping clients optimize their manufacturing processes and stay competitive. The company prioritizes long-term relationships, ensuring customers have access to expert advice and tailored solutions throughout their journey.
Competitive Pricing and Cost-Efficiency
Teeming offers cost-effective solutions without compromising quality, helping businesses maximize their return on investment. By delivering high-performance equipment at competitive prices, Teeming supports manufacturers in achieving their production goals while controlling costs.
Sustainability and Innovation
Teeming is committed to sustainable practices, incorporating energy-efficient technologies into its machines. This dedication to innovation not only benefits the environment but also provides customers with advanced tools that meet modern sustainability standards.
Contact Teeming Today
At Teeming Machinery, we're dedicated to helping you achieve precision and efficiency in your manufacturing processes. Our state-of-the-art laser welding technology and expert support services are designed to meet the needs of industries like automotive, aerospace, and medical device manufacturing.
Contact us today to learn how our innovative solutions can enhance your production capabilities and keep you ahead in a competitive market.